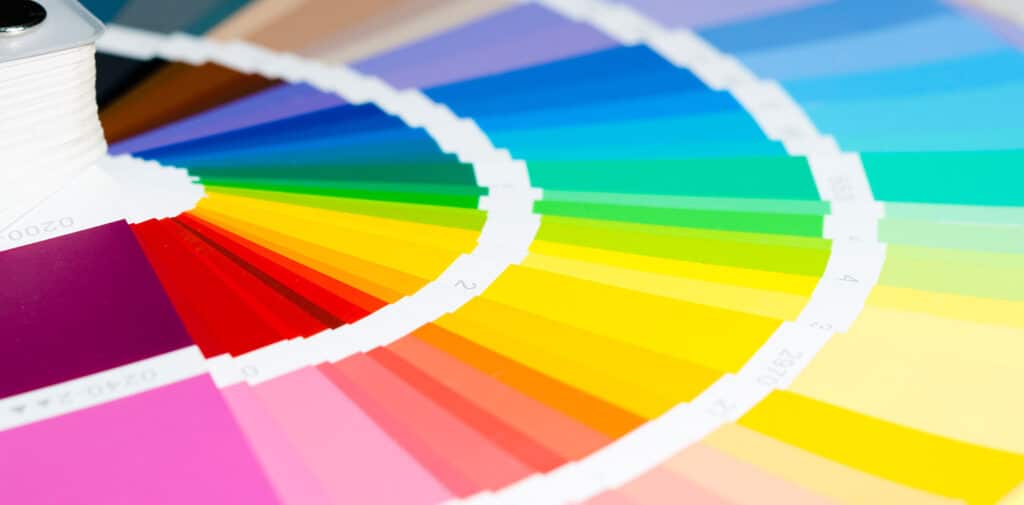
The Science of Color Matching in Silicone Rubber Production
Color matching in the manufacturing industry, especially when working with materials like liquid silicone rubber (LSR) and screen printing inks, is a critical and intricate process. Here at SiTECH, we pride ourselves on our precision and expertise in color matching, utilizing the Pantone Matching System (PMS), and the LAB color system to ensure consistency and accuracy.
The Pantone Matching System is a standardized color reproduction system widely used in various industries. It helps manufacturers and designers to ensure that colors match perfectly, regardless of the production process or material.
The LAB color system, also known as CIELAB, is an international standard for color measurement. Developed by the International Commission on Illumination (CIE), it’s designed to be a device-independent model that represents color universally, regardless of how it’s created. This system is particularly useful in industries where color precision is crucial.
LAB stands for:
L for Lightness, ranging from 0 (black) to 100 (white), representing the variable of brightness.
A and B for the color-opponent dimensions, with A representing the spectrum from green to red, and B representing the spectrum from blue to yellow.
In our color matching process, we utilize the LAB system alongside the PMS to achieve a ΔE (Delta-E) value of 1, ensuring minimal color difference perceivable by the human eye. The LAB system is particularly valuable because it considers the way humans perceive color, making it a more comprehensive approach to achieving true color accuracy.
For liquid silicone rubber, the color matching process is particularly challenging due to the material’s unique properties. LSR is known for its durability, flexibility, and stability across a wide range of temperatures and conditions. However, these same characteristics can affect how the color appears and behaves during the curing process. Our team of experts understands these variables and adjusts the color formulations accordingly to ensure that the final product matches the desired PMS color precisely.
Similarly, when dealing with screen printing inks, several factors can influence color accuracy, including the type of ink, the substrate, and the printing process itself. Our company uses high-quality inks and state-of-the-art printing technology to maintain color consistency. We also take into account the substrate’s color and texture, as these can significantly impact the appearance of the printed color.
In both cases, our color matching process involves a series of steps:
1. Understanding Client Needs: The journey begins with a detailed consultation to understand the client’s specific color requirements. We select the desired color from the PMS, which acts as our initial reference point.
2. PMS Reference: We identify the PMS code corresponding to the chosen color. This code serves as our baseline for the color matching process.
3. Translating to LAB Values: To enhance precision, we convert the PMS color into its LAB equivalent. The LAB system offers a more universal and exact color representation, crucial for the next steps.
4. Preliminary Color Mixing: Utilizing the latest technology available and our expertise in pigment and silicone rubber interactions, we create a preliminary color mix. This step is crucial, as it considers how pigments will behave and appear once mixed with silicone and cured.
5. Accurate Measurement with Spectrophotometry: Using a spectrophotometer, we measure the LAB values of our silicone rubber sample. This analysis reveals how close we are to the target color.
6. Iterative Color Adjustment: Based on the spectrophotometric data, we fine-tune the pigment mixture to align precisely with the target LAB values. This iterative process ensures the closest possible match.
7. Final Sample Production: Once the color is within a Delta-E (ΔE) of less than 1, indicating a near-perfect match, we produce a final sample for the client’s review.
8. Client Review and Approval: This crucial step involves presenting the final sample to the client, ensuring it meets their expectations in terms of color accuracy and material quality.
9. Consistency and Documentation: To guarantee consistency in mass production, we meticulously document the specific pigment formulation and process. This documentation is vital for quality control in large-scale manufacturing.
10. Mass Production: Armed with the approved color formulation, we proceed to mass produce the silicone rubber products, ensuring each batch adheres to the client-approved color standard.
This comprehensive process, blending PMS for initial color selection with the precision of the LAB system for fine-tuning, allows us to achieve an unparalleled level of color accuracy in silicone rubber products. Our commitment to this detailed approach is a testament to our dedication to quality and customer satisfaction. Here at SiTech, we understand the importance of color in branding and product design. A slight deviation in color can significantly impact customer perception and brand identity. That’s why we are committed to providing our clients with the most accurate color matching services in the industry. Our meticulous process and expertise in working with both liquid silicone rubber and screen printing inks make us a trusted partner for businesses looking to achieve perfect color consistency in their products.