Mold design is the most critical step in the production of silicone parts. But before you can start a mold design, it is important to know the basics. There are a few steps that need to be understood before starting every mold design. Here at Si-Tech we utilize liquid injection molding (LIM), so these steps will be for the LIM process.
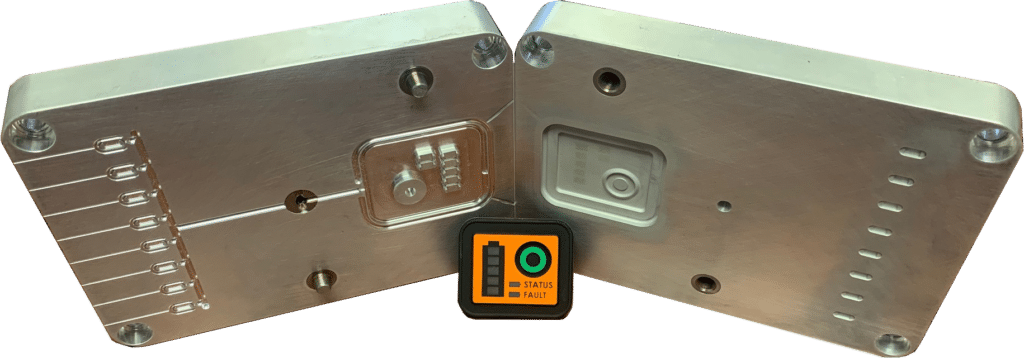
Step 1:
Gate Locations
Knowing the full scope of a silicone part and how it interacts within its assembly is important for us when designing a mold for any silicone keypad, gasket or component. This is particularly true for knowing where to place gate locations. Gates are where the silicone enters a mold cavity during the molding process. If avoidable, you will always want to place a gate location on a non-visible / non-critical side of a silicone part. Due to the nature of liquid silicone rubber, various gate types can be used. The two main types often used are direct gating and sub gating. Direct gating travels directly from a runner system into the mold cavity. Sub gating travels underneath the mold cavity to a desired location on the underside of the part.
Step 2:
Parting Lines
Similar to gate locations, it is also important to understand the full scope for parting line locations. A parting line occurs where the two mold halves meet. It is important to visually plan out the placement of the silicone part within the mold and where the parting line will occur prior to starting the actual design of a mold. Parting lines are typically where the most flashing will occur on a molded part. Due to this, you always want to try to have your parting lines located on non-critical and non-visible surfaces. Here at Si-Tech, we allow for 0.015” of flash on our silicone parts.
Step 3:
Shrinkage
Part shrinkage plays an important role in the silicone molding process. Silicone parts can shrink anywhere from 2-4% after molding. It is important to have a clear understanding on what secondary processes will need to occur, as well as where the part is being used. Some parts may need to be post-cured after the molding process which can increase the shrink percentage by as much as 1%.
Many decisions have to be made in the process of design and mold manufacturing for production of silicone components. At SiTECH, we are here to help make those decisions less daunting and more transparent. From our highly skilled engineers to our advanced silicone production equipment, our team is dedicated to the successful production of all your silicone mold rubber needs.