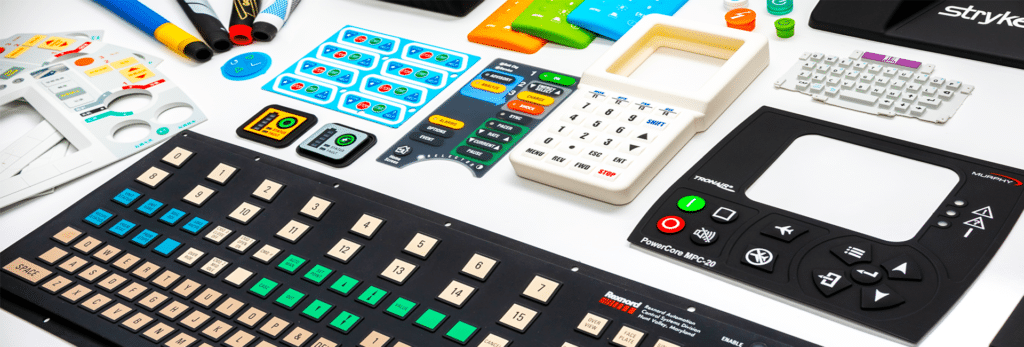
Advantages of Liquid Injection Molding (LIM) in Silicone Keypad Manufacturing
In today’s fast-paced manufacturing environment, precision, efficiency, and durability are essential. When it comes to producing silicone keypads, Liquid Injection Molding (LIM) has emerged as the go-to process for manufacturers looking to meet these high standards. From cost savings to design flexibility, LIM offers several advantages that make it the preferred choice for producing silicone keypads across various industries, including automotive, medical, military, and industrial applications.
In this blog, we’ll explore the key benefits of LIM and why it stands out as the ideal solution for silicone keypad manufacturing.
What is Liquid Injection Molding (LIM)?
Liquid Injection Molding (LIM) is a process used to manufacture silicone rubber parts by injecting a two-part liquid silicone rubber (LSR) compound into a mold. The liquid silicone material is precisely measured and mixed in a closed-loop system before being injected into a mold cavity, where it cures into a solid rubber part. This process is known for producing highly consistent and high-quality silicone components, ideal for keypads and other intricate parts.
Key Advantages of Liquid Injection Molding (LIM)
1. Precision and Consistency
One of the main benefits of LIM is the precision it offers in molding complex and intricate parts. Because LIM uses advanced machinery with tightly controlled injection parameters, manufacturers can create silicone keypads with consistent dimensions, tolerances, and surface finishes, ensuring high-quality parts every time.
For industries like medical devices and consumer electronics, where precision is critical, LIM ensures that every keypad meets exact specifications without variation from part to part. This consistency also contributes to a better tactile feel, which is essential in keypads where user interaction is a priority.
2. Faster Production Cycles
In today’s market, speed is crucial. LIM offers faster production cycles compared to other molding techniques such as compression molding. The closed-loop system used in LIM not only speeds up the injection process but also allows for faster curing times, meaning manufacturers can produce high volumes of parts more efficiently.
For customers needing rapid prototyping or high-volume production, LIM provides the ability to bring products to market faster without sacrificing quality or precision.
3. Reduced Waste and Cost Efficiency
Liquid Injection Molding is a highly efficient process, using precisely metered amounts of liquid silicone rubber. The closed-loop system ensures that material is used efficiently, reducing material waste and ultimately lowering production costs. Additionally, the precision of LIM minimizes the need for rework, further reducing costs related to production errors or inconsistencies.
In high-volume production environments, this waste reduction and cost efficiency can lead to significant savings over time, making LIM a smart choice for manufacturers looking to maximize their budget while maintaining quality.
4. Closed-Loop System for Cleaner Production
Unlike compression molding, where materials are often handled manually, LIM uses a closed-loop system that keeps the raw silicone material sealed throughout the production process. This minimizes the risk of contamination, making LIM ideal for industries such as medical devices and food-grade products, where cleanliness is paramount.
By keeping the material untouched and uncontaminated, LIM ensures that every silicone keypad meets stringent safety and quality standards, essential for both regulated industries and consumer-facing products.
5. Design Flexibility and Complexity
LIM offers exceptional design flexibility, making it easy to produce parts with complex geometries, thin walls, or intricate features that might be difficult or impossible with other molding techniques. For keypads, this means that manufacturers can easily integrate features such as backlighting, light pipes, or custom shapes and textures.
Additionally, LIM enables the integration of metal inserts, conductive carbon inserts, and custom backlighting solutions. This makes it possible to produce multi-functional keypads with enhanced durability, tactile feedback, and electrical conductivity, providing significant benefits to industries like automotive, telecommunications, and industrial control systems.
6. Durability and Performance
Silicone produced through Liquid Injection Molding offers excellent durability, with high resistance to extreme temperatures, chemicals, and environmental factors such as UV exposure and moisture. This makes LIM keypads suitable for rugged environments, including military and outdoor industrial applications, where reliability and long-term performance are essential.
The durability provided by LIM also extends the life cycle of silicone keypads, reducing the need for frequent replacements and ensuring that the product continues to perform as expected, even in harsh conditions.
Why Choose SiTech for Liquid Injection Molding?
At SiTech, we specialize in Liquid Injection Molding for silicone keypads and components. Our expertise in LIM allows us to provide precision-molded products that meet the highest standards of quality, consistency, and performance. With ISO 9001:2015 certification, our manufacturing process is designed to ensure that every product we deliver meets your exact specifications.
Whether you need rapid prototyping, custom design solutions, or high-volume production, SiTech’s LIM process delivers exceptional results tailored to your needs.
Liquid Injection Molding (LIM) is a highly efficient, precise, and cost-effective process that offers unparalleled advantages in silicone keypad manufacturing. Its ability to produce high-quality, durable, and customizable keypads makes it the preferred solution for industries that demand performance and reliability.
If you’re looking for a partner who can deliver innovative silicone keypads using the latest LIM technology, contact SiTech at 757-887-8488 or email sales@sitech-corp.com to learn more about how we can bring your project to life.